The best of both Man & Machine
Helios Solar has on its payrolls highly skilled engineers and staff. Our state of the art manufacturing facility in Bengaluru, India has been doling out premium solar modules
since its establishment in 2016.
Our production is semi-automated comprising the best in machinery imported from Europe & Asia thus achieving reliability in production quality.
We are able to produce a large number of top notch modules in a short span of time with great speed. Our harmonised production lines ensure efficiency. Our dust proof facilities help keep our products contamination free.
The best in quality management
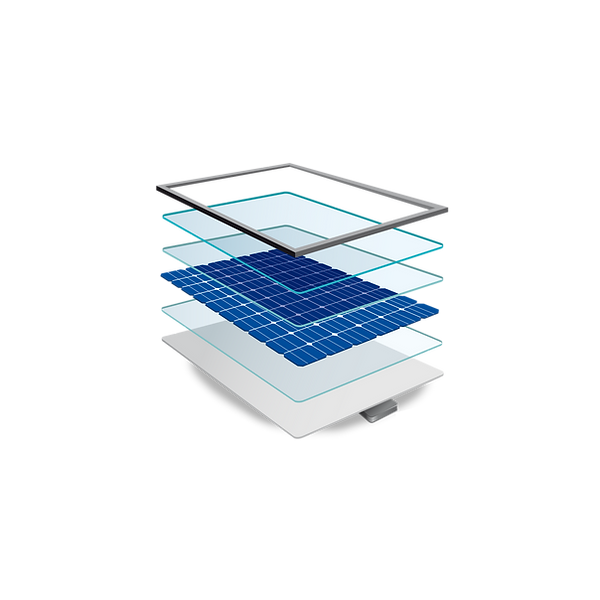
Al Frame - Deep anodized Aluminium frames which are resistant to corrosion and abrasion which enables protection from salt and mist corrosion
Glass - High transmission low iron,
tempered & PV grade glass
EVA Sheet - Fast cure, UV
stable EVA photovoltaic
encapsulant
Solar Cells - Cells employed
are of excellent low light and
optimal thermal co-efficient
performance
EVA Sheet - Fast cure, UV
stable EVA photovoltaic
encapsulant
Back Sheet – Tedlar based
back sheet for proven longer
life of modules
Junction Box – Fully potted IP67
JunctionBox with Schottkybypass
diodes having excellent thermal
stability
Our well trained line managers with over 10 years of experience in the field ensure care in every step of the process. They are always finding innovative solutions to the tough challenges posed in day to day processes and scaling up of production. Optimisation is their core ideology with due diligence provided to safety hence improving efficiency.
Making of Our Solar Modules
Tabbing & Stringing - The solar cells are assembled using the soldering process. The right temperature is maintained to prevent cracking during the soldering process and is a accurately time bound and measured process. This crucial step lends durability in the long run.
​
Lamination, Hot Press & Cool down - The lamination process where all the elements are placed one over the other and are pressed together to make the soul and heart of the PV Panel is the most critical step of the manufacturing process. The hot press stage heats and presses the elements at 155 degree Celsius for 10 mins to make all of them into one. Then the sandwiched component is cooled down to regular temperatures. The imported new generation SIEMENS Module Laminator used in this process inspires confidence and endows us to offer durability to our customers.
Taping & Framing - Once the lamination is completed the extrusions are shaved and the edges are taped using an adhesive tape on all sides. Then corrosion resistant aluminium is used to frame the pressed & cooled components giving it the needed sturdiness to withstand adverse weather conditions.
Junction, Testing & Packaging - A junction box is connected at the back of the framed panel which can be used to make further electrical connections. Then the module is sent for testing. It is ‘flashed’ under standard testing conditions to measure the power output. The modules which meet all the set quality standards are finally packed and sent to our customers.
​